Общая эффективность оборудования (OEE)
30 Авг 2009 Павел Рабунец в рубрике Lean в России и мире, О книгах, Рекомендуем | 11 комментариев
Просмотров: 49 907Общая эффективность оборудования (OEE — Overall Equipment Effectiveness) – это основной показатель всеобщего ухода за оборудованием (ТРМ). OEE отражает степень эффективности использования оборудования.
Насколько эффективно вы используете свое оборудование? Каковы потери, снижающие эффективность оборудования? Как с ними бороться?
На все эти вопросы поможет ответить расчет показателя Общей эффективность оборудования.
Для расчета ОЕЕ необходимо перемножить следующие показатели: производительность, готовность оборудования и качество. Эти показатели находятся следующим образом:
Готовность = Машинное время / Чистое рабочее время
Производительность = Текущая выработка / Запланированная выработка
Качество = Количество качественных изделий / Текущая выработка
Произведение этих элементов умножают на 100, таким образом полученный результат можно выразить в процентах:
ОЕЕ = Готовность x Производительность x Качество х 100
На следующем рисунке наглядно показано, как потери могут снижать общую эффективность оборудования, а также отражены элементы необходимые для расчета коэффициента OEE.
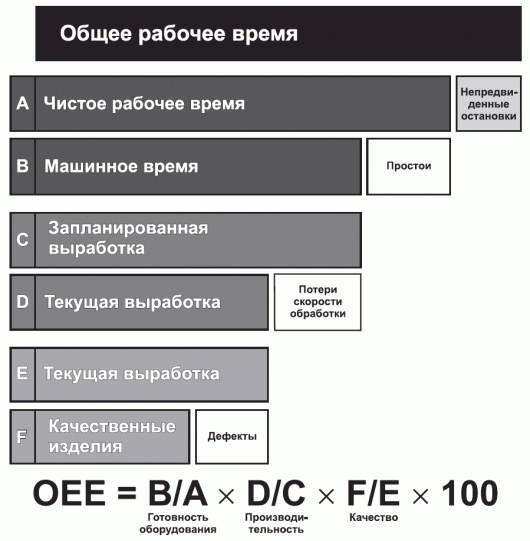
Элементы Общей эффективности оборудования (ОЕЕ) и потери, связанные с особенностями функционирования оборудования.
Измерение общей эффективности оборудования предполагает мониторинг того, как функционирует оборудование или протекает процесс. Определение ОЕЕ происходит на основе ежедневного фиксирования показателей, отражающих состояние оборудования, что способствует открытому подходу к обмену информацией и предотвращает случаи, когда плохое функционирование станков ставится в вину конкретному рабочему.
ОЕЕ является сбалансированным показателем, отражающим реальное положение дел, позволяющим улучшать производство и повышать прибыль предприятия.
Подробнее о показателе OEE и его использовании можно узнать в книге «Общая эффективность оборудования». Книга рекомендуется руководителям и сотрудникам предприятий в качестве руководства, содержащего полезные сведения о способах, которые помогут повысить эффективность работы оборудования.
В нашей lean-библиотеке доступен онлайн-просмотр этой книги. Пролистайте книгу по OEE бесплатно!
Рекомендую:
Необходимо ежедневно проверять оборудование
Бережливое производство в России и мире. Lean-карта
Концепция бережливого производства с оглядкой на русский менталитет
Производственная система Тойоты: уходя от массового производства
Система 5S — как улучшить своё рабочее место
Об авторе:
Подписывайтесь на Leaninfo.ru в соцсетях:
Или следите за новостями бережливого производства по email.
Смотрите также:
Оставить комментарий
Для отправки комментария вам необходимо авторизоваться.
Прекрасная книжка, доступна для чтения как руководителям разного уровня, так и рабочим.
Мы в своем произодстве используем аналогичный показатель ОПП (Оптимальный Показатель Производительности), концепция расчета та же, но учтена еще зависимость скорости машин от производимой номенклатуры.
А показатели ОПП (ОЕЕ) целесообразно внести в существующую систему Ключевых Показателей Эффективности, принятых в компании.
Хотел бы дополнить сообщение Сергея.
Царяпкин Сергей предложил использовать аналог OEE в виде оптимального показателя производительности (ОПП). Подробнее об этом можно прочитать в разделе «Формы документов» файлового хранилища портала LeanZone.ru. Там же есть примеры файлов в формате Excell, облегчающих расчет показателя OEE.
Компания ITM внедрила систему показателей OEE на заводе фирмы Валио под Москвой — см. например
http://www.astera.ru/pr/48119/
или на сайте http://www.itm.spb.ru
Предлагаю обсудить примеры успешного внедрения этой системы показателей в России, а также высказать мнение о том, на каких предприятиях это может быть востребовано в первую очередб.
Прочитал, со слов выглядит красиво. Интересно а TPM развернута на этом заводе Валио?
Вообще, автоматизация сбора и анализа ОЕЕ вещь необходимая, особенно при наличии большого станочного парка и большой номенклатуры выпускаемой продукции. А показатели эти нужны прежде всего (но не только) для совершенствования и развития TPM (всеобщей эксплуатационной системы). Также, эти показатели нужно рассчитать любому предприятию планирующему увеличение производственных мощностей, чтобы не покупать лишнего оборудования, хотя, опять же, если на предприятии не внедрены 5S, TPM, SMED, дзидока и стандартизация (как минимум!), OEE будет бессмысленным набором цифр.
Не думаю, что «если на предприятии не внедрены 5S, TPM, SMED, дзидока и стандартизация (как минимум!), OEE будет бессмысленным набором цифр».
Дело ведь прежде всего не в самих значениях OEE, а в их составляющих и их последующем анализе. Уверен, что OEE- это не показатель, а система показателей плюс методология, позволяющая находить узкие места. Но я писал о другом – не об очередном обсуждении теории, а о том, есть ли у кого-то конкретная практика работы с OEE. Или хотя бы явная потребность такую практику получить. То есть созрели ли российские предприятия до использования OEE, или еще нет…ПИШИТЕ!
Борис, если есть что предложить — пишите, рассмотрим. Отрасль — химия. С удовольствием съездил бы с Вами на похожее предприятие, нампример, в Европу где применяют ОЕЕ. К сожалению в России внятных предложений (с подтвержденной практикой) по развертыванию ОЕЕ я не встречал. Есть очень похожая методология RCM-2, родом она из Канады, по сути это ОЕЕ + TPM + ТОиР+SAP(c функционалом в области эксплуатации и обслуживания оборудования). Мы к ней активно присматриваемся.
ДМИТРИЮ КИМУ — Мои координаты bkatz@spectec.ru , b-katz@yandex.ru Напишите мне, пожалуйста, и сообщите, как с Вами связаться. Возможно, наш опыт Вас заинтересует.
ПРИОБРЕЛА КНИГУ.
ЧИСТОЕ ВРЕМЯ ЦИКЛА=ОБЩЕЕ РАБОЧЕЕ ВРЕМЯ — НЕПРЕДВИДЕННЫЕ ОСТАНОВКИ,
А ПО ТЕКСТУ УЖЕ: ОБЩЕЕ РАБОЧЕЕ ВРЕМЯ — ЗАПЛАНИРОВАННЫЕ ОСТАНОВКИ.
в ЧАСТИ РАСЧЕТА ГОТОВНОСТИ НЕ СОВСЕМ ПОНЯТНО ЧТО ЖЕ ВСЕТАКИ ВХОДИТ В «ЧИСТОЕ ВРЕМЯ».
В чистое время включается именно ВРЕМЯ РАБОТЫ ОБОРУДОВАНИЯ без учета остановок по разным причинам. А вот что включать в ОБЩЕЕ РАБОЧЕЕ ВРЕМЯ — это вопос методологии. Обычно в него включают, кроме чистого рабочего времени, только незапланированные остановки. Но можно — и запланированные тоже (плановые ремонты и ТО). Второй вариант позволяет учесть влияние стратегии ремонта. Скажем, чаще проводим плановое ТО — доступность несколько падает, но за счет увеличения скорости и уменьшения неплановых остановов OEE может возрасти…
Мне тоже непонятен принцип вычисления «Чистого времени» А и «Машинного времени» В.
Как раз из общего фонда рабочего времени вычитают плановые простои и получают плановое время работы. А вычитая из него уже внеплановые простои получают фактическое время работы, т.е. «машинное время» у вас. Поэтому непонятно, что понимается под «Простоями» у вас. Остаётся считать их плановыми простоями, но тогда формула получается с точностью до наоборот.
Если у вас поменять местами «Простои» (видимо плановые) и «Непредвиденные остановки», то тогда всё встаёт на свои места (кроме названий временных интервалов А и В).
О том же, кстати, подробная статья в википедии:
http://ru.wikipedia.org/wiki/OEE
Также, интервал С не стоит называть «Запланированной выработкой» — такое определение можно толковать по-разному. Лучше назвать его «(Технически) Максимально возможная выработка». Тогда всё становится однозначным.
коллеги, добрый день.
Ксли есть интерес к методологии RCM2 и ее применении на российских и зарубежных предприятиях, пишите. краткую информацию можно посмотреть на сайте eamsystems.ru ( в том числе запись семинара по RCM2.)